In the domain of 3D printing, the debate between resin and filament strength is a nuanced one, with each material bringing its own set of advantages to the table. Resins tout superior tensile strength, ideal for demanding applications, while filaments like Nylon and Polycarbonate excel in impact resistance, catering to a broader spectrum of project needs. The question remains: when faced with the choice between resin and filament strength, which material truly emerges as the champion? The answer lies in understanding the specific requirements of the project and how each material's unique properties can best serve those needs.
Resin Tensile Strength Comparison
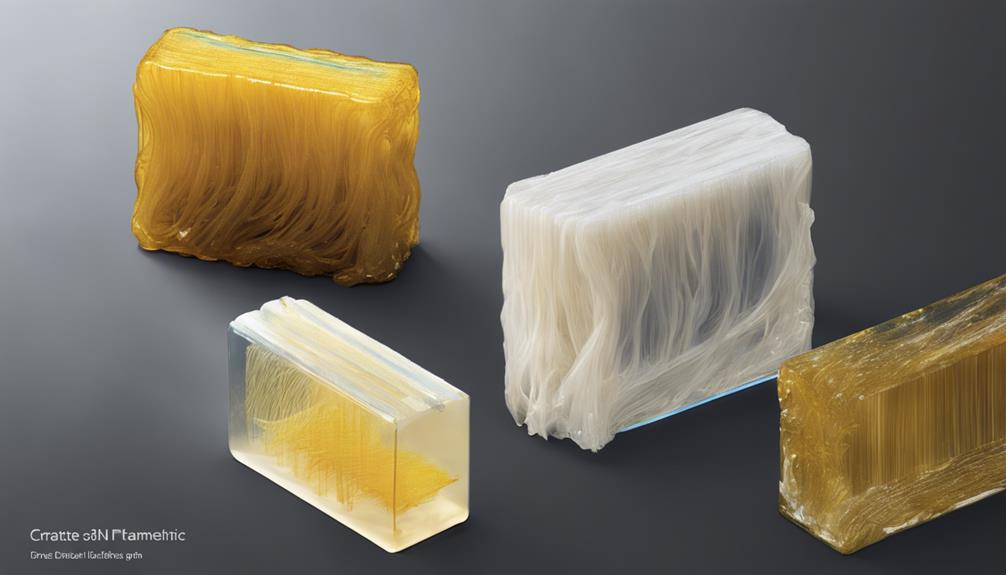
Comparing the tensile strength of different resin materials provides valuable insights into their mechanical properties and suitability for various applications. Among the materials commonly used in 3D printing, polycarbonate stands out with a tensile strength of 67.6 MPa, making it a robust choice for applications requiring high strength.
PLA follows closely behind at 64.4 MPa, offering good strength characteristics but with a tendency to decrease over time. PETG and Nylon exhibit slightly lower tensile strengths at 50.0 MPa and 48.3 MPa, respectively.
Understanding the tensile strength of these resin materials is essential for selecting the most appropriate material based on the specific requirements of the intended application.
Strength Comparison by Material
When evaluating material strength for 3D printing applications, it is essential to take into account the varying tensile characteristics of different materials. Tough Resin stands out as stronger than ABS, PETG, and Nylon. PLA held 285 pounds in a tensile strength test, but weakens over time. PETG, more flexible than PLA, resisted breaking in a bend test, showcasing its durability. ABS instantly snapped at 285 lbs in an ISO 527 test, indicating its brittleness. Polycarbonate, which requires high printing temperatures, held 685 pounds in a tensile strength test, highlighting its robust nature. Nylon's strength varies but generally surpasses ABS while falling below PLA, exhibiting bending at 485 lbs in a test, making it a versatile option for certain applications.
Resin Types and Impact Strength
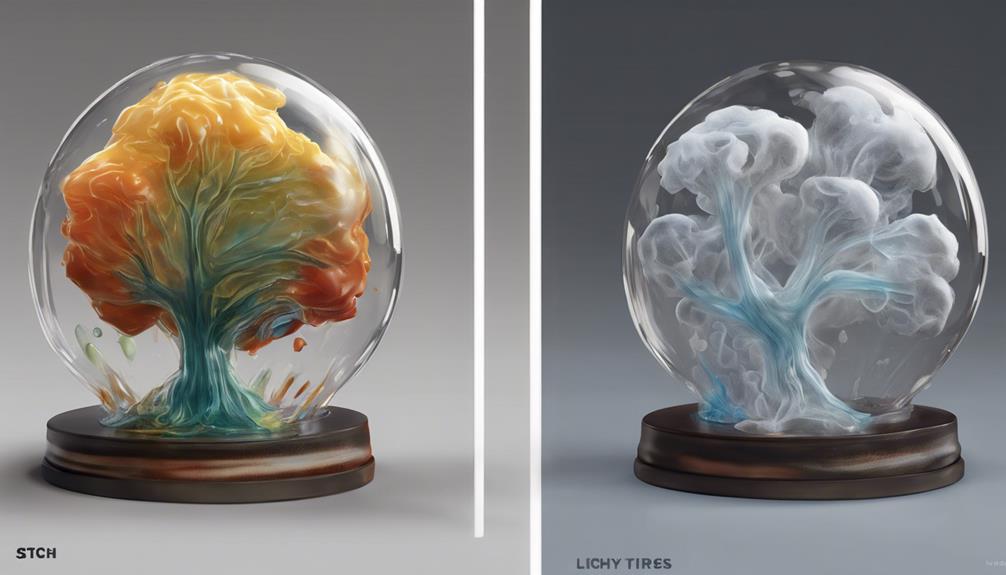
How do different resin types differ in impact strength and what are their implications for 3D printing applications?
Regular resin is known to be weak and unsuitable for outdoor use, while tough resin, such as Formlabs Tough 2000, eSuns Hard-Tough, and Siraya Techs Blu, is formulated to be strong, exhibiting double the tensile strength of regular resin.
In impact strength tests, tough resin has shown results of 280mJ, making it comparable to PLA and suitable for strong, isotropic prints.
This difference in impact strength between regular and tough resins highlights the importance of selecting the appropriate resin type based on the desired application and strength requirements in 3D printing projects.
Strongest Filaments Overview
In the domain of 3D printing material strength, polycarbonate stands out as one of the strongest filaments available, known for its exceptional durability and high thermal resistance.
When looking for the strongest filaments for your 3D printing projects, consider the following options:
- Nylon: Highly rated for strength, hygroscopic, and impact resistant.
- Polycarbonate: Rated as the strongest filament, with impressive thermal resistance capabilities.
- ABS: Known for its strength and impact resistance, although it is slightly weaker than polycarbonate when considering overall strength.
These filaments offer different strengths and properties, catering to various project requirements and printing needs.
Enhancing Part Strength Tips
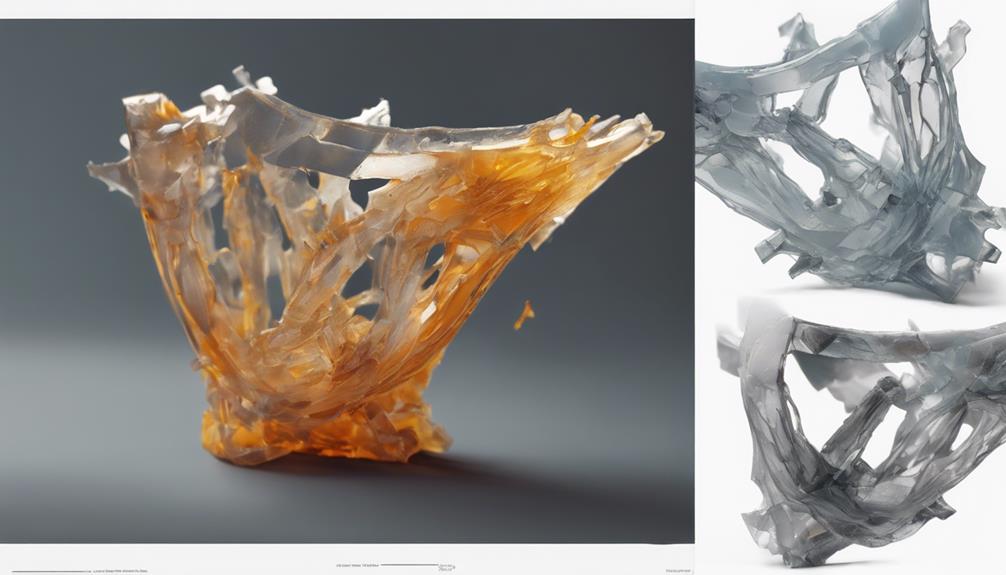
To optimize the strength of 3D printed parts, strategic implementation of reinforcement techniques plays an essential role in enhancing overall structural integrity.
Infill patterns have a substantial impact on part strength, with rectilinear or honeycomb patterns often recommended for their strength properties. Rectilinear patterns save plastic and reduce print time, ideal for one-directional strength, while honeycomb patterns offer strength from all directions.
Additionally, annealing can enhance firmness, heat resistance, and alter plastic characteristics, showing promising results particularly with PLA and PETG materials.
Understanding the application of the print, anisotropic versus isotropic properties, optimizing slicer settings, considering fabrication processes, and utilizing topology optimization are all key factors in further enhancing the strength of 3D printed parts.
Frequently Asked Questions
How Does Print Orientation Affect Part Strength?
Print orientation plays a crucial role in part strength. Proper orientation guarantees that the layers bear load effectively. Vertical printing boosts strength along the Z-axis but compromises strength in other directions. Optimizing orientation based on load distribution enhances overall part strength.
Is There a Correlation Between Layer Height and Strength?
Layer height directly influences part strength. Thinner layers enhance detail but may compromise strength. Coarser layers offer better strength at the expense of surface finish. Balancing layer height with structural requirements is essential for best part performance.
Can Post-Processing Techniques Improve Filament Strength?
Post-processing techniques such as annealing can enhance filament strength by improving firmness, heat resistance, and altering material characteristics. Understanding the impact of post-processing on specific filaments is essential for optimizing strength properties in 3D printed parts.
What Role Does Ambient Temperature Play in Part Strength?
Ambient temperature impacts part strength by influencing material properties. Extremes can cause warping or weakening, affecting mechanical performance. Proper environmental control during printing and post-processing is essential for the best part strength and dimensional stability.
Are There Specific Design Features That Enhance Print Strength?
Specific design features that enhance print strength include infill patterns like rectilinear or honeycomb for directional or all-direction strength respectively. Annealing can improve firmness, heat resistance, and material characteristics, while considering application, material properties, and fabrication processes is essential for optimized strength.
Conclusion
To sum up, the comparison between resin and filament strength in 3D printing reveals distinct advantages for each material. Resins like Tough Resin offer higher tensile strength, while filaments like Nylon and Polycarbonate excel in impact resistance.
Notably, Tough Resin has a tensile strength of up to 55 MPa, making it a reliable choice for applications requiring robust parts. Ultimately, the choice between resin and filament strength depends on the specific needs of the project.