Exploring the world of 3D printing precision reveals an essential yet intricate puzzle to solve – the persistent challenge of curling corners. In the quest for mastering the art of impeccable print quality, understanding the nuanced interplay between extruder calibration and hotend temperature adjustments stands as a pivotal milestone. However, the journey towards flawlessness doesn't end there. As we uncover the layers of complexities in achieving peak precision, a deeper exploration into filament selection strategies and expert insights promises a wealth of knowledge waiting to be discovered.
Understanding Curling Causes
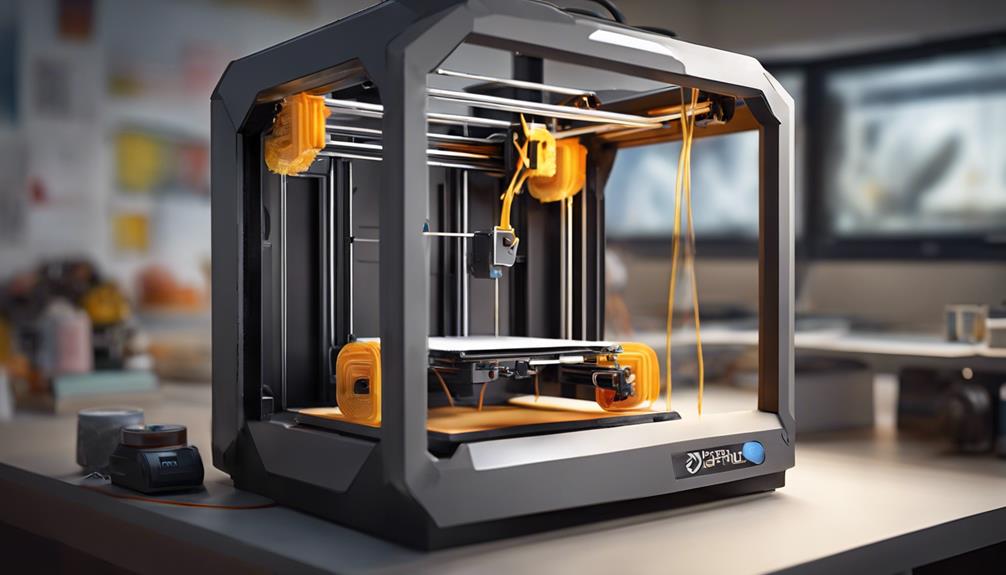
When delving into the complexities of 3D printing, understanding the causes of curling is paramount for achieving precise and flawless prints. Curling often results from material contraction in sharp areas of a print. While over-extrusion is a common culprit, it is not always the main cause.
Curling can lead to defects in the final print if not addressed appropriately. To combat this issue, adjustments to printing parameters such as hotend temperature settings can be essential. Lowering the nozzle temperature can help minimize material shrinkage time, while installing a layer fan can reduce cooldown times.
Fine-Tuning Hotend Temperatures
To enhance 3D printing outcomes, precise adjustment of hotend temperatures is essential, particularly in addressing issues like curling caused by material contraction.
When fine-tuning hotend temperatures, it is vital to find the delicate balance between ensuring proper material flow and preventing issues like warping and curling. Raising the hotend temperature excessively may mask underlying problems but can result in defects such as curling. It is advisable to use the lowest viable temperature to minimize material shrinkage time and avoid overheating the filament.
Brightness in PLA prints can indicate if the temperature is too high. Ideal temperatures should be determined through testing, and adjustments should be made accordingly to achieve the desired printing results without compromising the quality of the final product.
Mastering Extruder Calibration
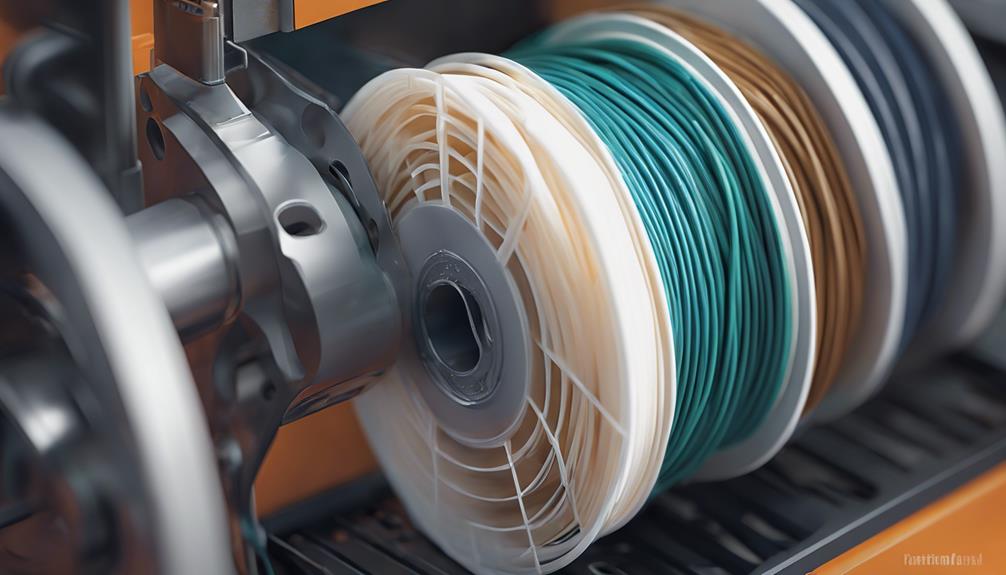
Extruder calibration mastery is vital for achieving precise and consistent 3D printing results. Calibrating the extruder steps guarantees the exact amount of material required is provided. This step is essential in controlling the filament volume and achieving accurate prints.
After extruder calibration, adjusting the flow rate becomes necessary to fine-tune the printing process further. Flow rate adjustments should be tailored to the specific material being used to optimize the printing outcome.
Following the recommended instructions for testing with tools like a caliper or micrometer is essential for accurate calibration. By mastering extruder calibration and flow control, 3D printing enthusiasts can enhance the precision and quality of their prints.
Choosing Filament for Precision
Selecting the ideal filament type is paramount for achieving precise and high-quality 3D prints. When choosing filament for precision, consider the following:
- PLA: Known for low shrinkage ratio, making it easier to print.
- PETG: Requires a heated bed but has low shrinkage.
- Nylon: Significant shrinkage, needs enclosed printers.
- ABS: Shrinks significantly, leading to warping without a heated bed.
- Considerations: Properly leveling the bed and enclosing the printer can reduce warping.
Careful selection of filament type is essential to mitigate common printing issues and ensure successful 3D prints.
Expert Recommendations and Insights
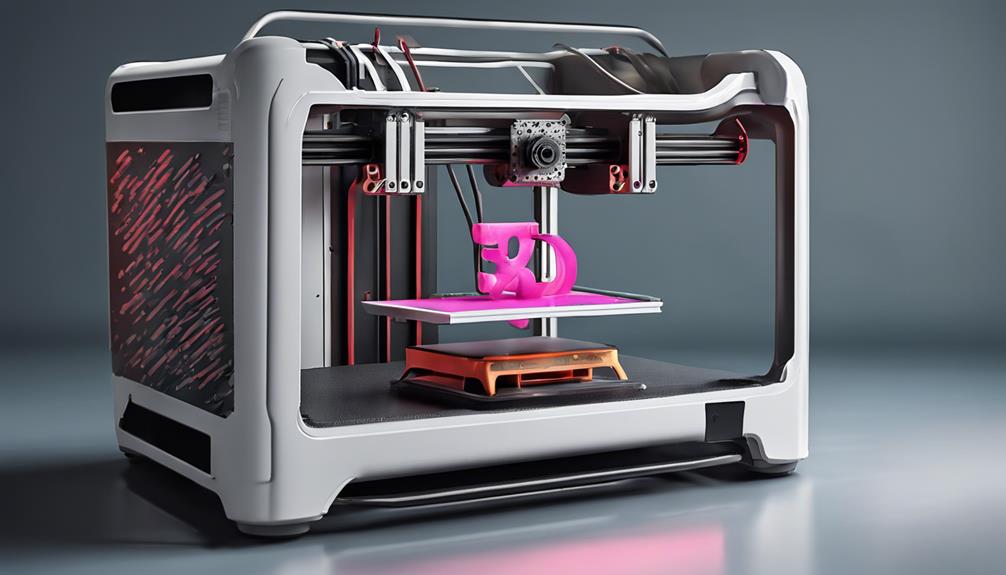
With years of experience in the 3D printing field, Martin Mayer provides valuable recommendations and insights for enthusiasts looking to master precision in their prints. Martin emphasizes the importance of fine-tuning printing parameters, extruder calibration, and understanding filament types for successful outcomes. Below are key insights and recommendations from Martin Mayer:
Printing Parameters | Extruder Calibration | Filament Types |
---|---|---|
Adjust hotend temperature for curling issues. | Calibrate extruder steps accurately. | Consider materials with low shrinkage like PLA. |
Use layer fan to reduce cooldown time. | Control filament volume through flow rate adjustments. | PETG offers low shrinkage but requires heated bed. |
Test and optimize temperature settings. | Vary flow rate based on material type. | ABS and nylon shrink significantly, requiring enclosed printers. |
Frequently Asked Questions
How Can I Prevent Warping When Printing Sharp Corners?
To prevent warping when printing sharp corners, adjust nozzle temperature, install a layer fan, or reduce speed. Ensuring proper bed adhesion, increasing bed temperature, or enclosing the printer are effective solutions. Calibrate extruder steps and control flow rate for precise printing.
What Are the Signs of Overextrusion in 3D Prints?
What are the signs of overextrusion in 3D prints? Overextrusion manifests as excessive material deposition, leading to rough surfaces, oozing, and loss of print detail. Address by adjusting flow rate, calibrating extruder steps, and monitoring print quality.
Is It Necessary to Adjust Flow Rate After Extruder Calibration?
Adjusting flow rate post extruder calibration is essential to control filament volume accurately. It allows fine-tuning for different materials, ensuring top-notch printing results. Follow calibration with flow rate adjustments to enhance print quality and precision.
How Does Filament Type Affect the Precision of 3D Prints?
Filament type greatly influences 3D print precision. For example, PLA's low shrinkage ratio offers easier printing, while ABS requires a heated bed to avoid warping. Understanding these materials' behaviors is essential for achieving top-notch print quality and functionality.
Can You Recommend Specific Upgrades for Advanced 3D Printing?
For advanced 3D printing, consider upgrading to a dual extruder system for multi-material prints, a high-resolution LCD screen for enhanced user interface, and a direct drive extruder for better filament control. These upgrades can optimize your printing capabilities.
Conclusion
To sum up, mastering the calibration of extruder steps and fine-tuning hotend temperatures are essential for achieving precise 3D prints and eliminating curling corners.
By understanding the causes of curling, adjusting hotend temperatures, and choosing the right filament, users can greatly enhance print quality and accuracy.
An interesting statistic to note is that by properly calibrating extruder steps, users can improve print accuracy by up to 20%.