When exploring the intricate world of dual extrusion printing, mastering infill settings and tackling oozing can be akin to solving a complex puzzle. Understanding how to optimize infill density, fine-tune retraction, and adjust temperatures holds the key to achieving flawless dual extrusion prints. However, there's an essential element that often goes unnoticed, a secret technique that can greatly elevate your dual extrusion game. Curious to uncover this game-changing method that can transform your prints?
Common Dual Extrusion Printing Issues
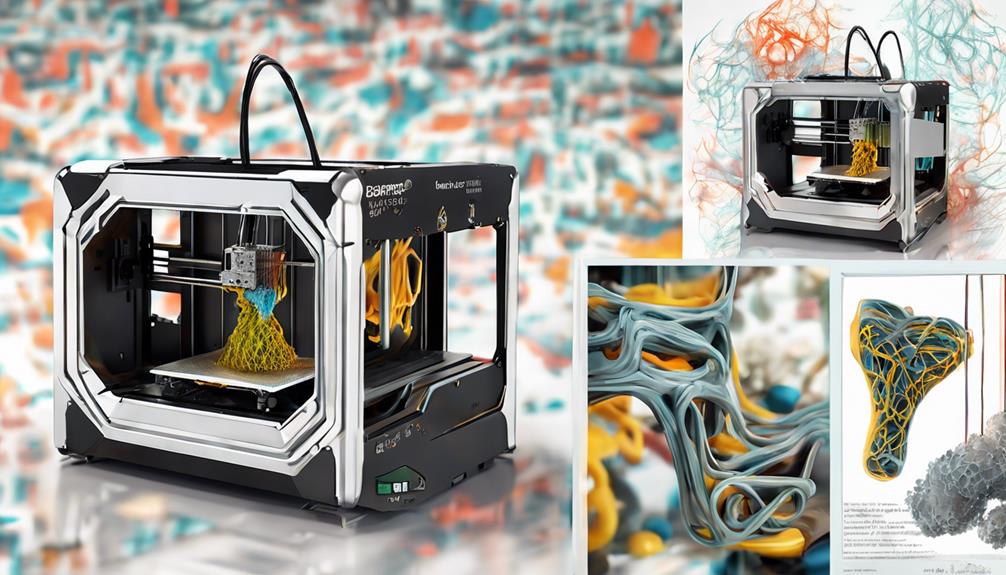
Wondering what challenges you might encounter when diving into the world of dual extrusion printing? Common issues include oozing and stringing caused by filament leakage, layer shifting leading to misaligned prints, and hardware problems like loose screws and stretched belts contributing to shifting layers.
Keep an ear out for clicking sounds from motors as they can indicate misalignment. Adjusting printing speed can impact layer alignment, so be mindful of that.
To tackle these problems, consider using a prime tower to reduce oozing and under extrusion, and an ooze shield to prevent color bleeding and stringing. Fine-tuning settings like Prime Tower and Ooze Shield can greatly enhance your dual extrusion printing experience.
Slicing Software Configuration for Dual Extrusion
When configuring slicing software for dual extrusion, make sure to set up your extruders and assign models accurately to optimize your printing process. Begin by adding your printer model and configuring the dual extruder setup in software like Cura, Simplify3D, or Ideamaker.
Define which extruder corresponds to each nozzle and guarantee the correct assignment of models to respective extruders. This step is vital for achieving successful dual extrusion prints without color bleeding or misalignment issues.
Techniques for Improving Print Quality
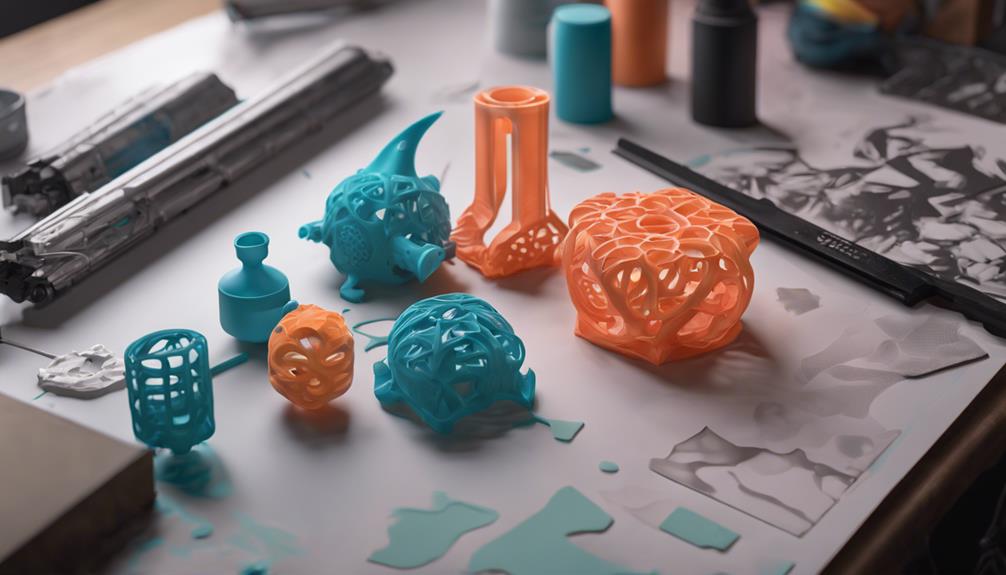
To enhance the quality of your dual extrusion prints, consider adjusting infill settings and addressing oozing issues effectively.
Increasing infill density can improve the strength and stability of your prints, especially for intricate designs. Experiment with different infill patterns like honeycomb or gyroid to find the best balance between strength and material usage.
Additionally, adjusting the infill overlap percentage can help reduce gaps between infill lines, resulting in smoother surfaces.
To combat oozing, fine-tune retraction settings to minimize filament leakage during tool changes. Implementing a coasting feature can also help reduce oozing by stopping extrusion slightly before the end of a perimeter.
Troubleshooting Overlapping in Dual Extrusion
For ideal dual extrusion printing results, make sure to properly manage overlapping volumes to troubleshoot potential issues effectively.
When dual extruders overlap during printing, it can lead to imperfections like gaps, blobs, or uneven surfaces in your 3D models.
To troubleshoot overlapping in dual extrusion, adjust settings such as outline overlap, wall thickness, printing speed, infill pattern, volume, density, and temperature.
Experiment with these settings to find the right balance that minimizes overlap issues while maintaining print quality.
Final Tips for Oozing and Infill Fix
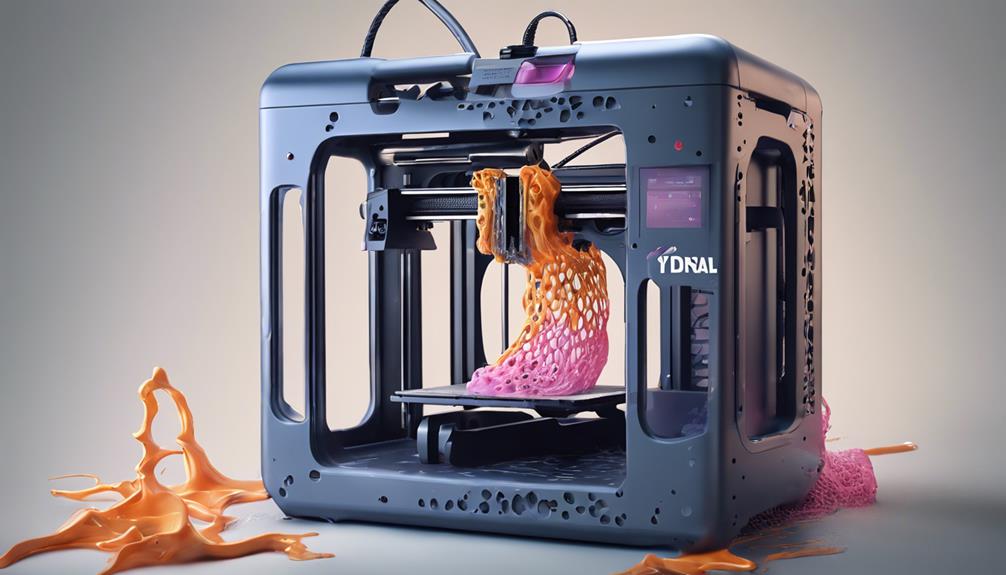
Consider implementing these final tips to address oozing and infill issues in your dual extrusion printing projects:
- Retraction Settings: Adjust retraction distance and speed to minimize oozing between extrusions.
- Temperature Calibration: Fine-tune temperatures for both filaments to reduce oozing and improve adhesion.
- Infill Density: Increase infill density to enhance part strength and reduce gaps in dual extrusion prints.
- Cooling Fan Control: Utilize cooling fans strategically to solidify layers faster and combat oozing issues.
Frequently Asked Questions
How Can I Prevent Nozzle Oozing During Dual Extrusion Printing?
To prevent nozzle oozing during dual extrusion printing, adjust retraction settings in your slicing software, ensuring filaments retract properly when not in use. This helps minimize oozing between extrusions, leading to cleaner prints.
What Are Some Common Hardware Issues Affecting Dual Extrusion Prints?
When you embark on dual extrusion prints, watch out for pesky hardware gremlins like loose screws and stretched belts causing misaligned layers. Don't let these troublemakers ruin your masterpiece; tighten up for smooth sailing.
Is There a Specific Way to Adjust Printing Speed for Dual Extrusion?
Adjust your printing speed for dual extrusion by fine-tuning settings in slicing software like Cura or Simplify 3D. Experiment with different speeds to optimize layer alignment and reduce issues like oozing and misalignment for higher quality prints.
How Do I Address Misalignment Indicated by Clicking Sounds During Printing?
Address misalignment during printing by tightening loose screws and belts. Adjust printing speed for better alignment. The clicking sounds indicate misalignment; guarantee all components are secure. Keep an eye on hardware for peak performance.
What Steps Can I Take to Troubleshoot Layer Shifting in Dual Extrusion Prints?
To troubleshoot layer shifting in dual extrusion prints, check for loose screws, belts, and adjust printing speed. Confirm that settings like wall thickness, infill, and temperature are correct. Addressing hardware issues and adjusting parameters can prevent misalignment.
Conclusion
You've learned how to master infill and oozing fix in dual extrusion printing.
Did you know that by adjusting retraction settings, you can reduce filament oozing by up to 80%?
Keep fine-tuning your settings, experimenting with temperatures, and utilizing cooling fans to achieve peak print quality.
With these techniques, you'll be able to create cleaner and more precise dual extrusion prints every time.
Happy printing!