When it comes to 3D printing, did you know that choosing the right infill pattern can increase the strength of your prints by up to 40%? Understanding how different patterns affect the structural integrity of your creations is key to achieving peak performance. By exploring the intricate relationship between infill patterns, density, and printing time, you can open up a world of possibilities to enhance the strength of your 3D printed objects. Curious to discover how to maximize the full potential of your prints?
Strength Levels of Infill Patterns
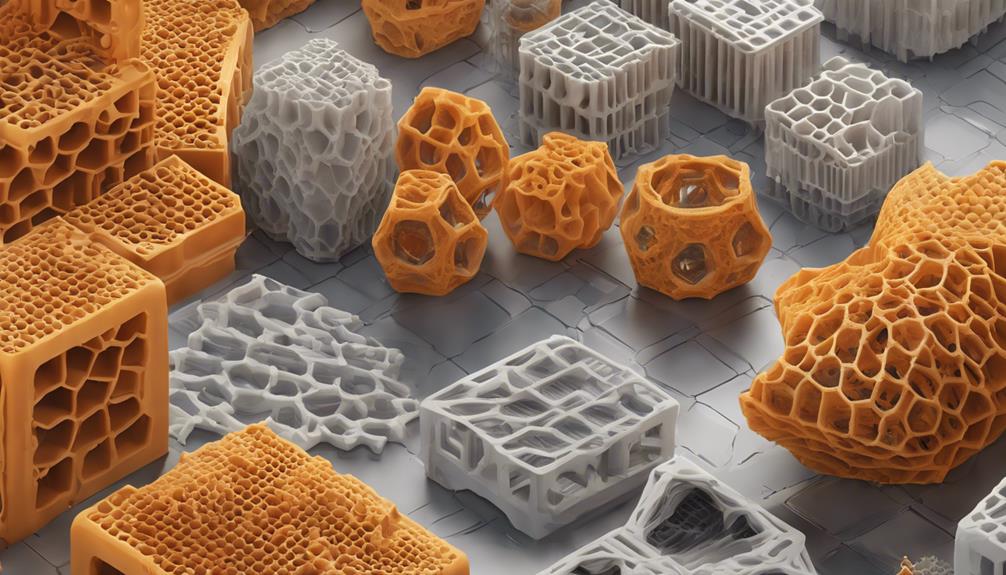
In order to determine the most effective strength levels of infill patterns in 3D printing, it's essential to take into account various factors such as pattern geometry and material usage efficiency. Different infill patterns offer varying degrees of strength.
Low strength patterns like Lines and Zig-Zag are quick to print but not suitable for heavy vertical loads. Medium strength patterns such as Grid and Triangles provide better strength but consume more material and time. For high-strength needs, Cubic and Octet patterns offer robustness from all directions.
Ultimately, choosing the right infill pattern involves balancing strength requirements with printing time and material efficiency. Make informed decisions based on the specific needs of your 3D printed object.
Impact of Infill Density on Strength
Consider the significant influence of infill density on the strength of your 3D prints. The density of infill directly correlates with the strength of your printed parts. Ideal strength with efficient material usage is often achieved at infill densities between 20-50%. Beyond 50% infill density, the increase in strength becomes less significant, leading to diminishing returns. Parts exceeding 75% infill density may add unnecessary weight without substantial strength benefits. It is important to find the right balance between infill density, strength, and material consumption to optimize your 3D prints.
Infill Density | Strength Level |
---|---|
0-20% | Low |
20-50% | Ideal |
50-75% | Diminishing |
75-100% | Excessive |
Relationship Between Infill Patterns and Printing Time
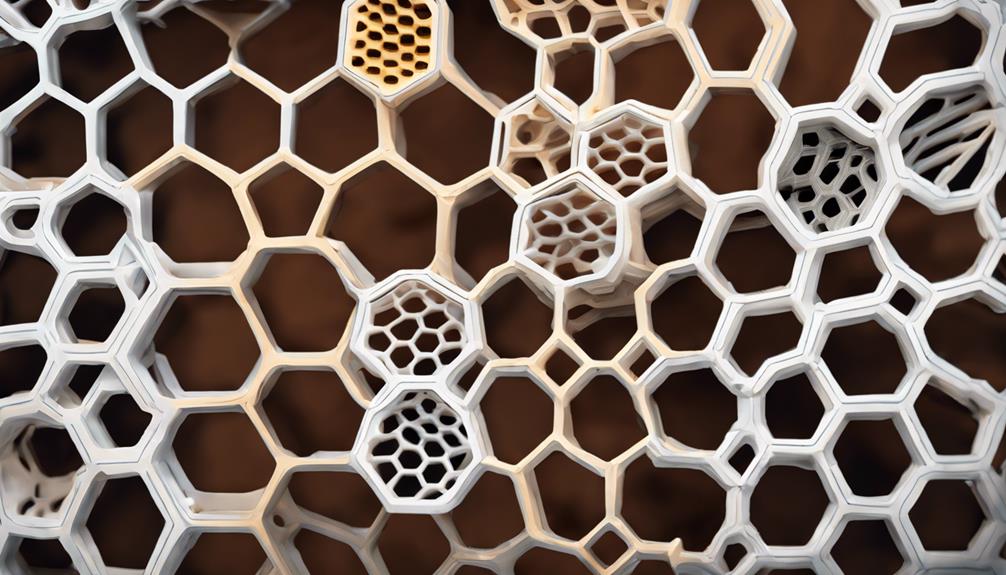
With the influence of infill density on strength established, understanding how different infill patterns impact printing time is essential for optimizing your 3D printing process.
The choice of infill pattern greatly affects the time it takes to complete a print. Patterns like Lines and Zig-Zag are quicker but offer lower strength, while patterns like Cubic or Gyroid take longer to print but provide higher strength.
Factors such as pattern complexity and the number of directional changes impact the overall printing time.
Key Factors Influencing Print Strength
To enhance the strength of your 3D prints, prioritize adjusting layer height, modifying infill percentage, and experimenting with different print orientations. Factors like filament type, quality, print orientation, number of perimeters, and layer height play vital roles in determining the strength of your prints. Choosing the right filament based on its properties is essential for print durability. Print orientation affects layer adhesion and overall print strength, while the number of perimeters/shells greatly impacts print strength, often more than infill patterns.
Factors Influencing Print Strength | Importance |
---|---|
Filament type and quality | High |
Print orientation | Medium |
Number of perimeters | High |
Strategies for Enhancing Print Strength
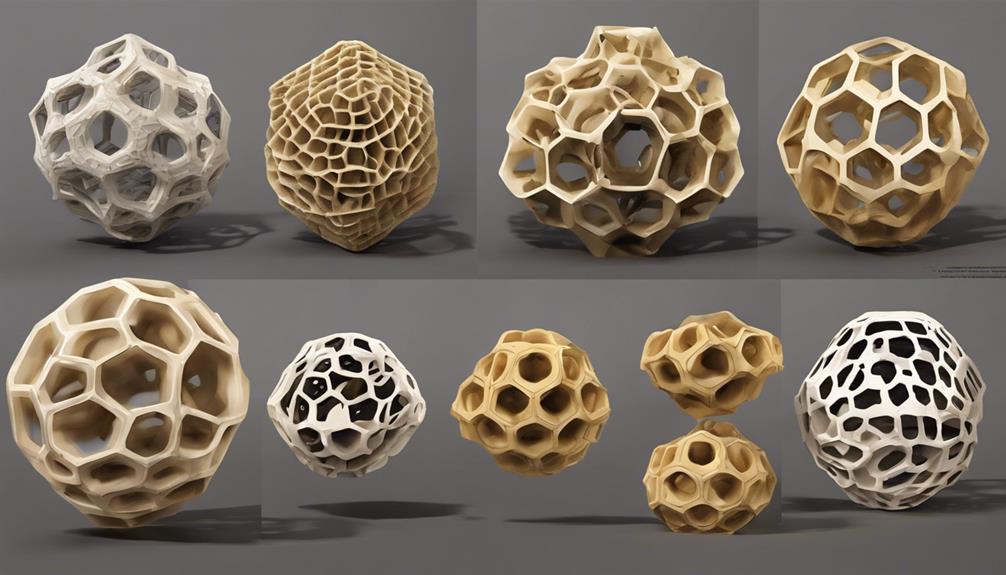
When aiming to boost the strength of your 3D prints, focus on implementing specific strategies to enhance print durability and structural integrity. Adjusting the layer height can positively impact strength, ensuring a better bond between layers.
Modifying the infill percentage, choosing patterns like Cubic or Gyroid for best strength, and customizing print orientation all contribute to enhancing print robustness. Consider annealing the print by heating it to the glass shift temperature for improved strength properties.
Remember to select the right filament type and quality, as well as adjusting the number of perimeters and layer height, to further enhance the overall strength of your 3D prints. By carefully considering these strategies, you can significantly increase the durability and reliability of your printed objects.
Importance of Filament Selection
How important is selecting the right filament type for maximizing the strength of your 3D prints? Filament selection plays a vital role in determining the durability and strength of your final prints.
Different filaments offer varying properties such as flexibility, impact resistance, and tensile strength. For top-notch strength, consider filaments like PETG or ABS known for their sturdiness. PETG provides excellent layer adhesion and impact resistance, while ABS offers high temperature resistance and durability.
On the other hand, PLA, although easy to print with, may not offer the same strength benefits. Hence, when aiming for robust prints, choosing the appropriate filament type is essential in achieving the desired strength and durability in your 3D prints.
Considerations for Optimal Print Orientation
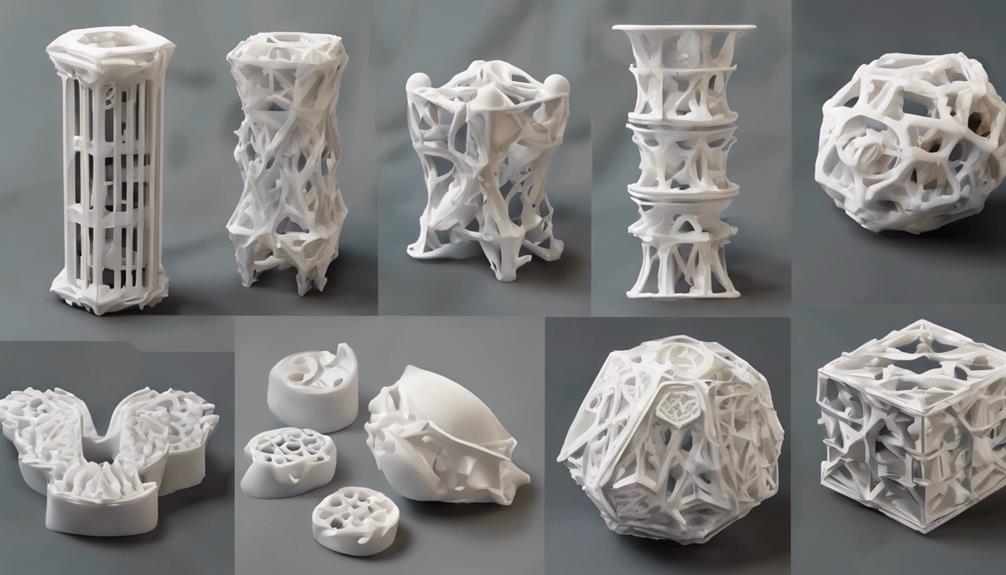
Considering the most favorable print orientation can greatly impact the strength and quality of your 3D prints. Ideal orientation guarantees that the layers are aligned in the direction of the applied forces, enhancing structural integrity.
By selecting the right orientation, you can minimize weak points, improve layer adhesion, and enhance overall part strength. Additionally, orienting your print correctly can reduce the need for support structures, saving time and material.
Experiment with different orientations to find the one that best suits your design and intended application. Remember, print orientation is a vital factor in maximizing the strength and durability of your 3D printed objects.
Make sure to take the time to assess and select the most effective orientation for each print.
Frequently Asked Questions
Can Infill Patterns Affect the Flexibility of 3D Printed Objects?
Infill patterns impact the flexibility of 3D printed objects. Options like lines or zig-zag offer low flexibility, while cubic or gyroid patterns provide higher flexibility. Adjust infill patterns based on desired object durability and usage.
How Does Print Speed Vary Between High and Low Infill Density?
When printing with high infill density, your speed decreases due to the intricate structure. Low infill density speeds up printing by using less material. Adjusting density affects speed, striking a balance between quick prints and sturdy objects.
Do Different Filament Colors Impact the Strength of Prints?
Different filament colors do not impact print strength to a large extent. Focus on factors like infill patterns, density, and print settings for strength optimization. Experiment with settings to find the right balance for your prints.
Can Infill Patterns Influence the Overall Weight of a 3D Print?
When choosing infill patterns, remember: lighter patterns decrease weight but may compromise strength. Opt for stronger infills like Cubic or Gyroid for durability. Balancing weight and strength guarantees ideal 3D print performance.
Is There a Maximum Limit to the Number of Perimeters for Print Strength?
When aiming for best print strength, consider that adding more perimeters can enhance durability, but there is a limit. Beyond a certain point, additional perimeters may not greatly increase strength and could slow down printing.
Conclusion
You've learned how different infill patterns can impact the strength of your 3D prints. By adjusting infill density and choosing the right pattern, you can maximize strength without adding unnecessary weight.
Did you know that using a Cubic infill pattern can boost the strength of your prints by up to 30% compared to a Zig-Zag pattern? Experiment with these tips to harness the ultimate strength potential in your 3D printed objects!