Did you know that by strategically adjusting infill strategies, 3D printing can achieve up to 60% reduction in material usage while maintaining structural integrity? This innovative approach to infill customization not only optimizes resource utilization but also enhances the overall performance of printed objects. Discover how varied infill strategies can revolutionize the world of 3D printing by elevating the quality and functionality of your creations.
Infill Optimization Techniques
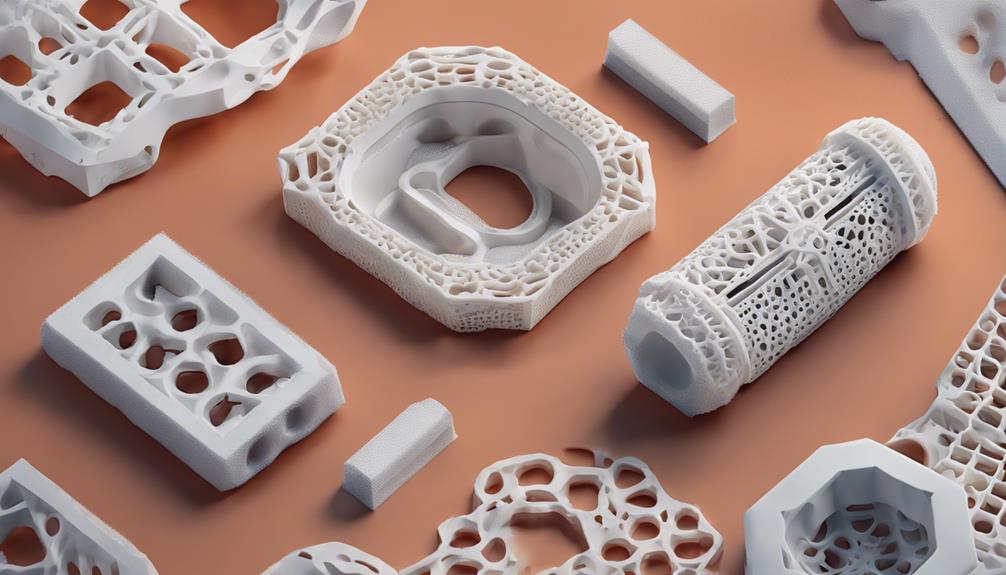
To enhance your 3D printing outcomes, mastering infill optimization techniques is essential. Understanding infill density and pattern selection is vital for achieving the desired balance between strength, rigidity, weight, appearance, cost, and print time.
By adjusting infill settings, you can maximize the efficiency of material usage while ensuring the structural integrity of your prints. Experimenting with different infill patterns, such as lines, honeycomb, grid, and more, allows you to tailor the internal structure to meet specific requirements. Variable infill density further enhances your flexibility in optimizing different areas of your print.
Exploring Variable Density Benefits
As you explore the benefits of variable infill density, you'll uncover the significant advantages it offers in enhancing the structural integrity and efficiency of your 3D prints. By adjusting the infill density in specific areas, you can reinforce critical sections of your prints while conserving material in less essential areas.
This customization not only optimizes the strength and rigidity of your prints but also reduces print time and material usage. Variable infill density empowers you to tailor the internal structure of your models to meet specific requirements, resulting in more robust and cost-effective prints.
Embracing this strategy allows you to achieve a balance between strength and efficiency, producing high-quality 3D prints tailored to your exact needs.
Maximizing Pattern Efficiency
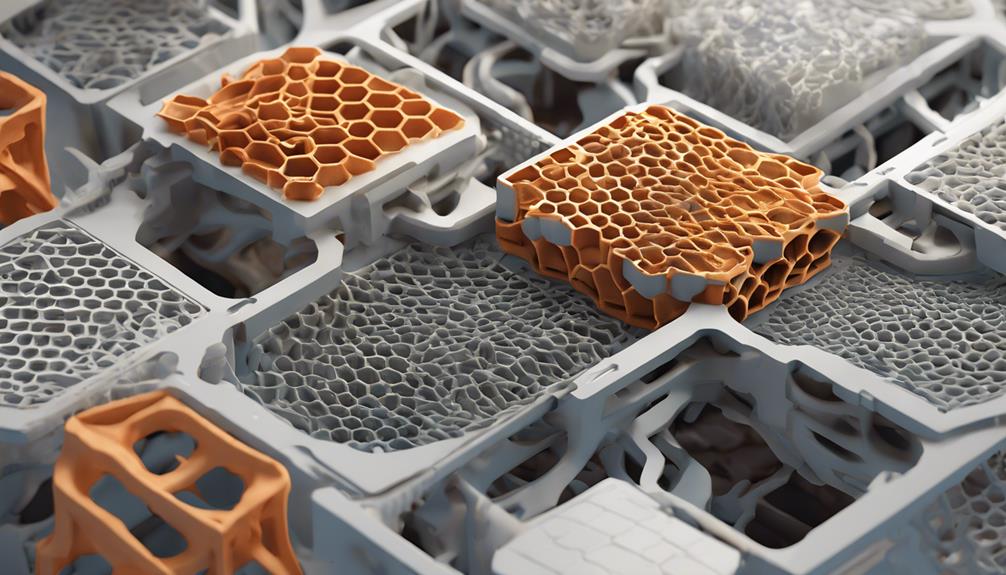
Enhance the efficiency of your 3D printing patterns by strategically selecting and optimizing infill designs that align with your specific print requirements.
- Understand Pattern Functions: Analyze the purpose of your print to choose the most suitable infill pattern.
- Consider Material Efficiency: Opt for patterns that use material effectively to minimize waste and reduce printing costs.
- Evaluate Strength Requirements: Select patterns that enhance structural integrity based on the intended use of the printed object.
- Balance Speed and Quality: Find a pattern that strikes the right balance between print time and the desired finish for your project.
Enhancing Structural Integrity
Maximize the structural integrity of your 3D prints by strategically incorporating infill patterns that align with your design specifications and functional requirements. To enhance strength, consider using infill patterns like Gyroid, which offer excellent load-bearing capabilities.
Honeycomb patterns distribute weight evenly, increasing stability. Tri-Hexagon infills provide a balance between strength and material efficiency.
By choosing the right infill pattern, you can reinforce specific areas prone to stress, ensuring the overall durability of your print. Experiment with different infill densities to further fortify critical sections.
Advanced Infill Customization

Explore advanced techniques for customizing infill to elevate your 3D printing projects to new levels of precision and efficiency.
- Optimized Infill Density: Adjust infill density for specific areas to enhance strength and reduce material usage.
- Combining Infill Patterns: Merge different infill patterns within a single print for varied structural integrity and visual appeal.
- Variable Infill Strategies: Employ multiple infill patterns and densities throughout your print to tailor properties as needed.
- Utilizing Support Blockers: Enhance customization by utilizing support blockers in slicer software to control infill placement in intricate designs.
Frequently Asked Questions
Can Infill Patterns Be Customized Beyond the Options Provided in Cura?
Yes, you can customize infill patterns beyond Cura options by designing and implementing your own patterns through advanced slicer settings or specialized software. Tailoring infill to suit specific needs enhances print quality and functionality.
How Does Infill Density Impact the Overall Surface Finish of a Print?
Infill density acts like the paintbrush strokes on a canvas, impacting the print's surface finish. Higher density yields smoother surfaces, while lower density can reveal the layer lines. Finding the right balance transforms your print quality.
Is It Possible to Combine Multiple Infill Patterns for Different Sections of a Model?
Yes, you can combine multiple infill patterns for different sections of a model. It allows optimizing strength, appearance, and material usage. Varying infill patterns in specific areas enhances structural integrity and efficiency. Experiment to find the best combination.
What Considerations Should Be Made When Adjusting Infill for Flexible Filament Prints?
When adjusting infill for flexible filament prints, consider tweaking density for balance between flexibility and support. Opt for patterns like Gyroid for enhanced flexibility. Experiment with different settings to find the best results for your project.
Are There Any Tools or Plugins to Simulate Infill Strength Before Printing?
When adjusting infill for 3D prints, consider tools like plugins for simulating infill strength pre-printing. These resources aid in predicting structural integrity, allowing you to optimize settings for ideal strength and material efficiency.
Conclusion
You've just scratched the surface of 3D printing possibilities with varied infill strategies. By exploring different infill density and patterns, you've opened up a world of structural optimization and efficiency.
Embrace the power of customization and experimentation to elevate your prints to new heights. Revolutionize your 3D printing game with tailored properties and precise control over internal structures.
The future of 3D printing is in your hands, ready to be shaped and molded with infinite possibilities.